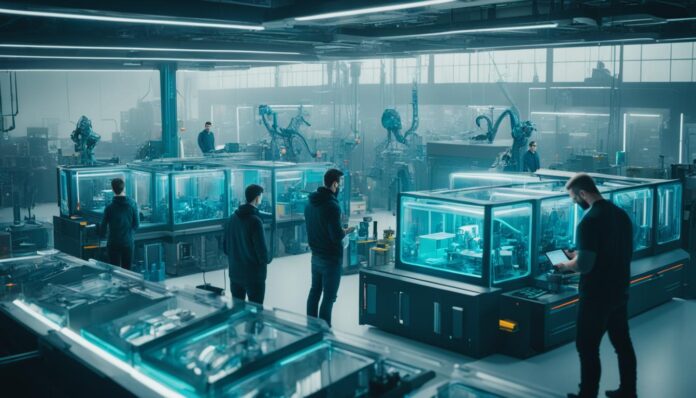
3D printing, also known as additive manufacturing, has gained significant popularity in recent years, revolutionizing the manufacturing industry. The concept of 3D printing dates back to the 1980s when it was first introduced as a rapid prototyping technology. However, it is only in the past decade that 3D printing has gained widespread recognition and adoption in various industries, including industrial 3D printing, digital fabrication, on-demand production, supply chain optimization, customized manufacturing, and sustainable production.
Key Takeaways
- 3D printing has evolved from a rapid prototyping technology to a versatile manufacturing solution.
- Customization and on-demand production are key benefits of leveraging 3D printing in manufacturing.
- 3D printing can optimize supply chains and enable localized manufacturing.
- 3D printing offers potential for weight reduction and improved material efficiency in manufacturing.
- 3D printing is being widely adopted in industries such as aerospace, automotive, and healthcare.
The Evolution of 3D Printing in Manufacturing
The history of 3D printing can be traced back to the 1940s, when the concept of additive manufacturing was first described. In 1945, sci-fi author Murray Leinster described a machine that could “make drawings in the air” and output plastic parts layer-by-layer in his short story “A Logic Named Joe.” However, it took a few more decades for this vision to become reality.
Early Prototyping: The Origins of 3D Printing
As the 1990s and 2000s progressed, the industry saw rising adoption and usage of additive manufacturing for rapid prototyping across automotive, aerospace, medical, consumer goods, and other industries. Both established corporations and startups expanded the capabilities of 3D printing during this period.
From Rapid Prototyping to End-Use Parts
The impact of 3D printing on various industries is significant. In the healthcare industry, 3D printing has revolutionized medical device manufacturing by enabling the production of customized implants and prosthetics. In the aerospace industry, 3D printing has been used to create lightweight components that improve fuel efficiency and reduce emissions.
The Growth of Additive Manufacturing Across Industries
Additive manufacturing and industrial 3D printing have seen widespread adoption across a variety of manufacturing industries, from 3D printing applications in aerospace and defense to healthcare and automotive. As the technology continues to evolve, the potential for 3D printing to transform manufacturing processes and product development is vast and promising.
How can I leverage 3D printing in manufacturing by 2025?
One of the key advantages of 3D printing is its ability to create customized products. Traditional manufacturing methods often involve producing large quantities of identical products, which may not meet the specific needs or preferences of individual customers. With 3D printing, each product can be easily customized to meet the unique requirements of each customer, enabling customization and on-demand production of personalized products.
Supply Chain Optimization and Localized Manufacturing
Another way that 3D printing can be leveraged in manufacturing is through supply chain optimization and localized manufacturing. Traditional manufacturing methods often involve transporting raw materials and finished products over long distances, resulting in significant carbon emissions and logistical challenges. By leveraging 3D printing, companies can decentralize their production and move it closer to the point of consumption, reducing the environmental impact and improving the efficiency of the supply chain.
Weight Reduction and Material Efficiency
3D printing also offers the potential for weight reduction and improved material efficiency in manufacturing. Traditional manufacturing methods often involve the removal of material to create the desired shape, resulting in significant waste. In contrast, 3D printing is an additive process, where material is added layer by layer to create the final product, minimizing waste and maximizing material utilization. This can lead to more sustainable production practices and reduced environmental impact.
Applications of 3D Printing in Manufacturing
The aerospace and defense (A&D) industry is one of the earliest adopters of 3D printing, with the first use of the technology going back to 1989. Now, three decades later, A&D represents a 16.8% share of the $10.4 billion additive manufacturing market and heavily contributes to ongoing research efforts within the industry. 3D printing has enabled the creation of lightweight components and spare parts for aircraft, reducing weight and improving fuel efficiency. Aerospace and defense companies are increasingly leveraging 3D printing to accelerate prototyping and on-demand production of customized components.
Automotive and Transportation
The automotive and transportation industries have also seen significant adoption of 3D printing technology. Similar to the aerospace industry, 3D printing is being used to produce prototypes, tooling, and customized components for vehicles. Automakers and transportation companies are harnessing the power of 3D printing to create spare parts on-demand, reducing inventory costs and lead times. The ability to produce customized components has also opened up new opportunities for personalized vehicles and transportation solutions.
Healthcare and Medical Devices
The healthcare industry has been a significant beneficiary of 3D printing technology, particularly in the production of customized medical devices and implants. 3D printing has revolutionized the way prosthetics and orthotic devices are manufactured, allowing for the creation of customized, comfortable, and highly functional solutions for patients. Additionally, 3D printing has enabled the production of patient-specific surgical guides, implants, and even personalized organ models for pre-surgical planning and training.
Conclusion
As you’ve learned, 3D printing is poised to revolutionize the manufacturing industry by 2025 and beyond. This remarkable technology offers a multitude of advantages, from enabling personalized, on-demand production to optimizing supply chains and enhancing material efficiency.
In the aerospace and defense sector, 3D printing is already being utilized to create lightweight components and spare parts, improving fuel efficiency and reducing emissions. Likewise, the automotive and transportation industries are leveraging 3D printing to produce customized components and streamline their supply chains.
Perhaps most significantly, the healthcare industry has been a prime beneficiary of 3D printing, with the technology enabling the creation of personalized medical devices, implants, and prosthetics. As 3D printing continues to evolve, the potential for transformative impacts across various sectors is truly exciting.
By embracing the power of 3D printing, you can position your manufacturing operations for success in the years to come. Explore the possibilities, unlock new levels of customization, and optimize your supply chain – the future of manufacturing is here, and it’s powered by the remarkable capabilities of 3D printing.
FAQ
How can 3D printing be leveraged in manufacturing by 2025?
3D printing, also known as additive manufacturing, offers several key advantages that can be leveraged in manufacturing by 2025 and beyond. Some of the ways you can leverage 3D printing include:
- Enabling customization and on-demand production of products to meet the unique needs of individual customers
- Optimizing supply chains and enabling localized manufacturing to reduce transportation costs and environmental impact
- Achieving weight reduction and improved material efficiency in manufacturing through the additive process of 3D printing
What is the history of 3D printing?
The concept of 3D printing dates back to the 1940s, when the idea of additive manufacturing was first described. However, it wasn’t until the 1980s that 3D printing was introduced as a rapid prototyping technology. Over the past decade, 3D printing has gained widespread recognition and adoption across various industries, including aerospace, automotive, and healthcare.
How has 3D printing impacted different industries?
3D printing has had a significant impact on several industries:
- In the healthcare industry, 3D printing has revolutionized the production of customized implants and prosthetics.
- In the aerospace industry, 3D printing has enabled the creation of lightweight components that improve fuel efficiency and reduce emissions.
- In the automotive industry, 3D printing is being used to produce prototypes, tooling, and customized components for vehicles.
How can 3D printing improve supply chain optimization and localized manufacturing?
3D printing offers the potential to optimize supply chains and enable localized manufacturing. Traditional manufacturing methods often involve transporting raw materials and finished products over long distances, resulting in significant carbon emissions and logistical challenges. With 3D printing, products can be manufactured closer to the end-user, reducing transportation costs and environmental impact.
How can 3D printing contribute to weight reduction and material efficiency in manufacturing?
One of the key advantages of 3D printing is its ability to create products through an additive process, where material is added layer by layer to create the final product. This is in contrast to traditional manufacturing methods, which often involve the removal of material to create the desired shape, resulting in significant waste. 3D printing can lead to weight reduction and improved material efficiency in manufacturing, making it a more sustainable production method.